Curo
A modular, repairable, and adhesive-free sneaker designed for sustainability
Curo is a casual, lifestyle sneaker that has been designed in a way that all parts can be repaired and replaced as required, rather than disposing of the entire shoe. All parts can be easily separated from each other as no adhesives have been used within the product. The goal was to create a sneaker that reduced the impacts of the footwear industry on the environment.
Individual Project - 2020-2021 (Capstone Project)
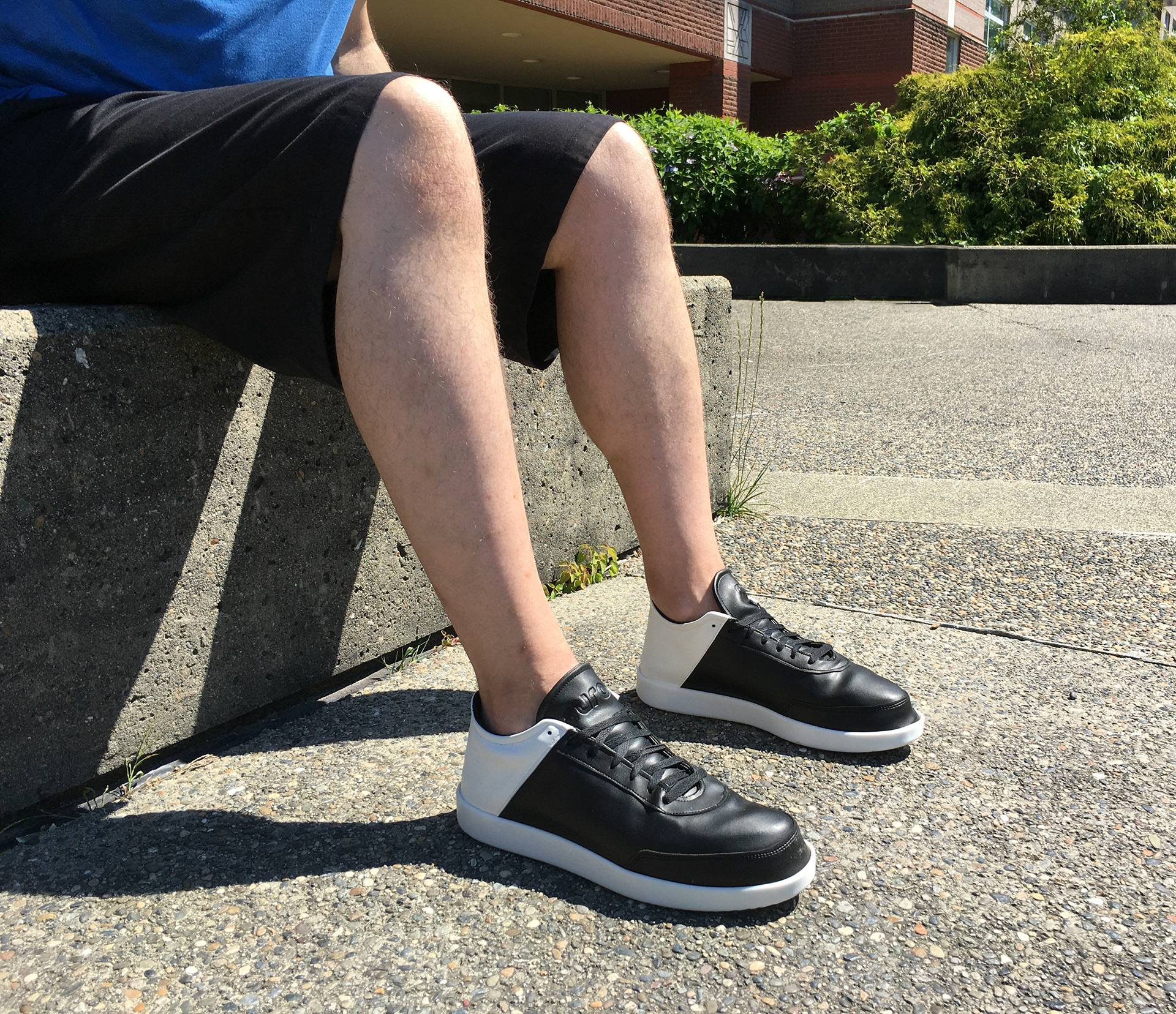

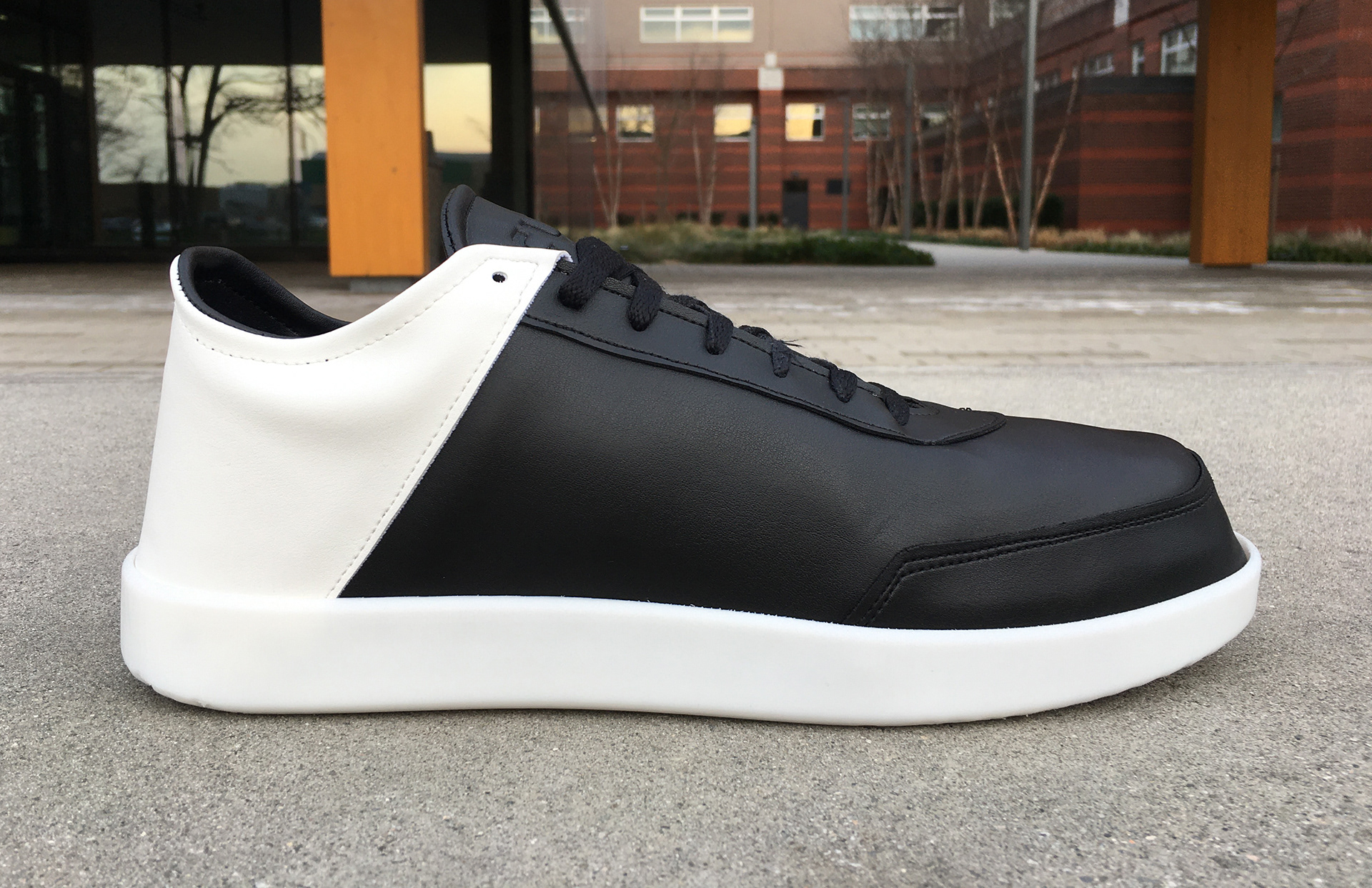
Product Overview
A quick breakdown of the components
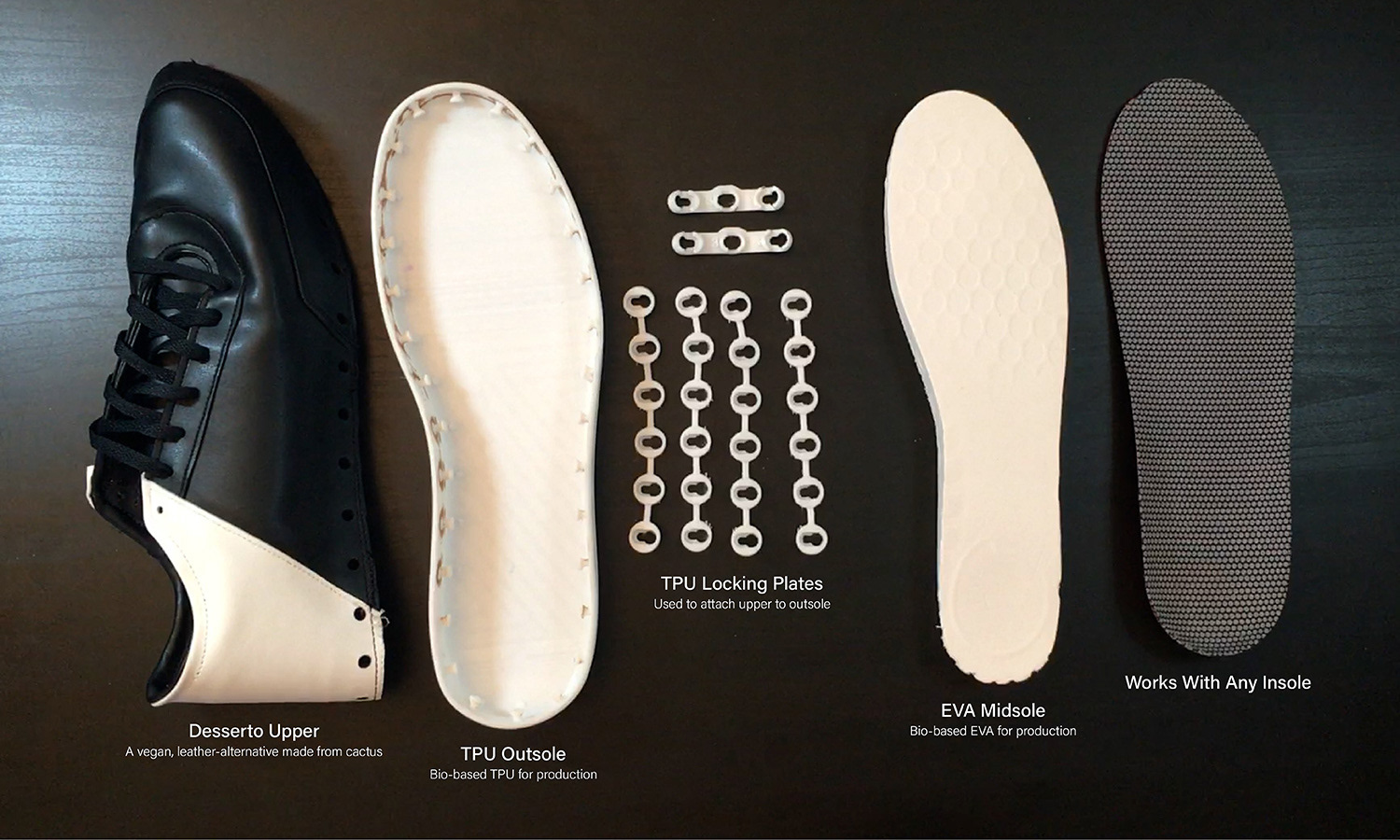
Assembly
A short video showing the components and assembly process
Problem
What are the impacts of the footwear industry?
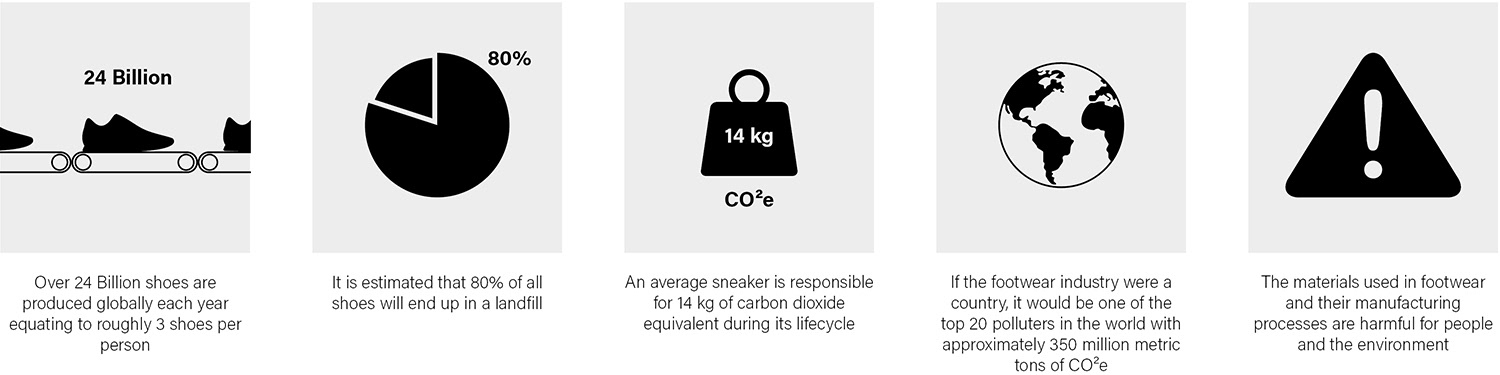
Research for this project was extensive. A summary can be found on my research website which includes sources for the statistics. The page can be viewed at wordpress.kpu.ca/sneakers/
Market research was also conducted to analyze the sustainable sneakers that are already on the market as well as some modular or repairable alternatives.
Points of Wear
What are the common areas of a sneaker that wear out or need repair?
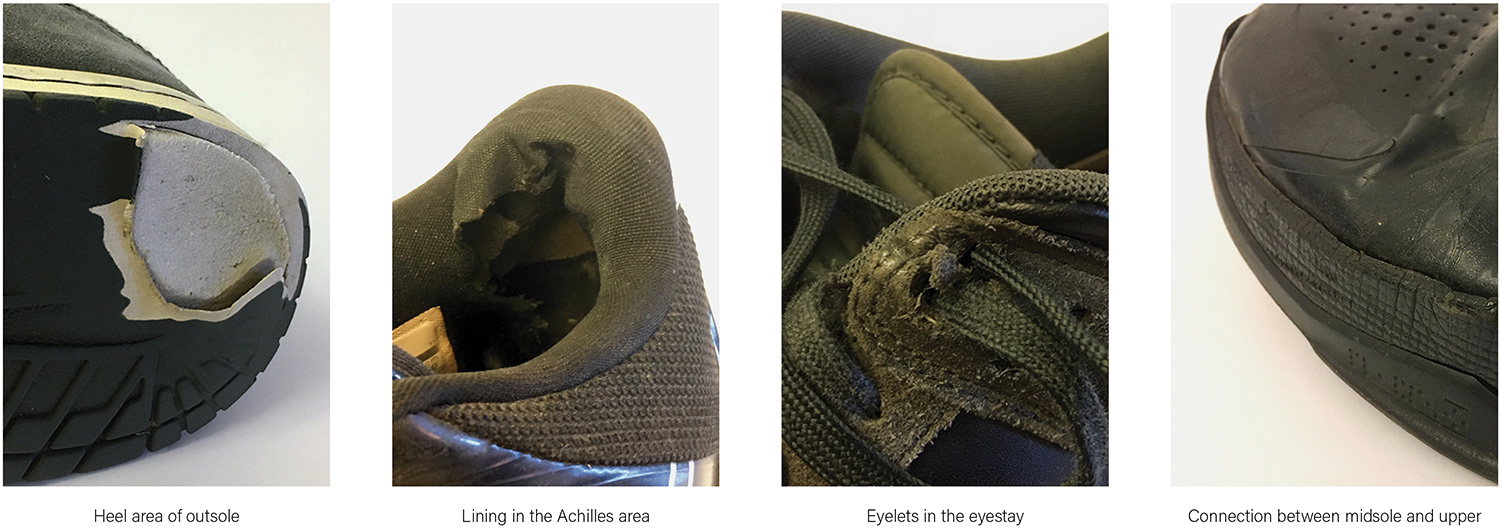
Key Takeaways
A short list of knowledge gained from the research phase
- Footwear production increases each year, a 21.2% increase since 2010
- This is approximately 2% growth per year; the world population grows by 1% per year
- Fast-fashion reduces attachment to sneakers and makes it easier to throw them away
- Most sneakers are monstrous hybrids and are not separated at end of life
- The environmental impacts and contributions to global warming cannot be ignored
- Material changes alone do not make enough impact on the CO₂e from sneakers
- Shoes need to last longer so that fewer need to be produced
- A sneaker could last longer by increasing the durability and/or by making it repairable
- This is approximately 2% growth per year; the world population grows by 1% per year
- Fast-fashion reduces attachment to sneakers and makes it easier to throw them away
- Most sneakers are monstrous hybrids and are not separated at end of life
- The environmental impacts and contributions to global warming cannot be ignored
- Material changes alone do not make enough impact on the CO₂e from sneakers
- Shoes need to last longer so that fewer need to be produced
- A sneaker could last longer by increasing the durability and/or by making it repairable
Possible Design Pathways
What are the possible directions this project could take?
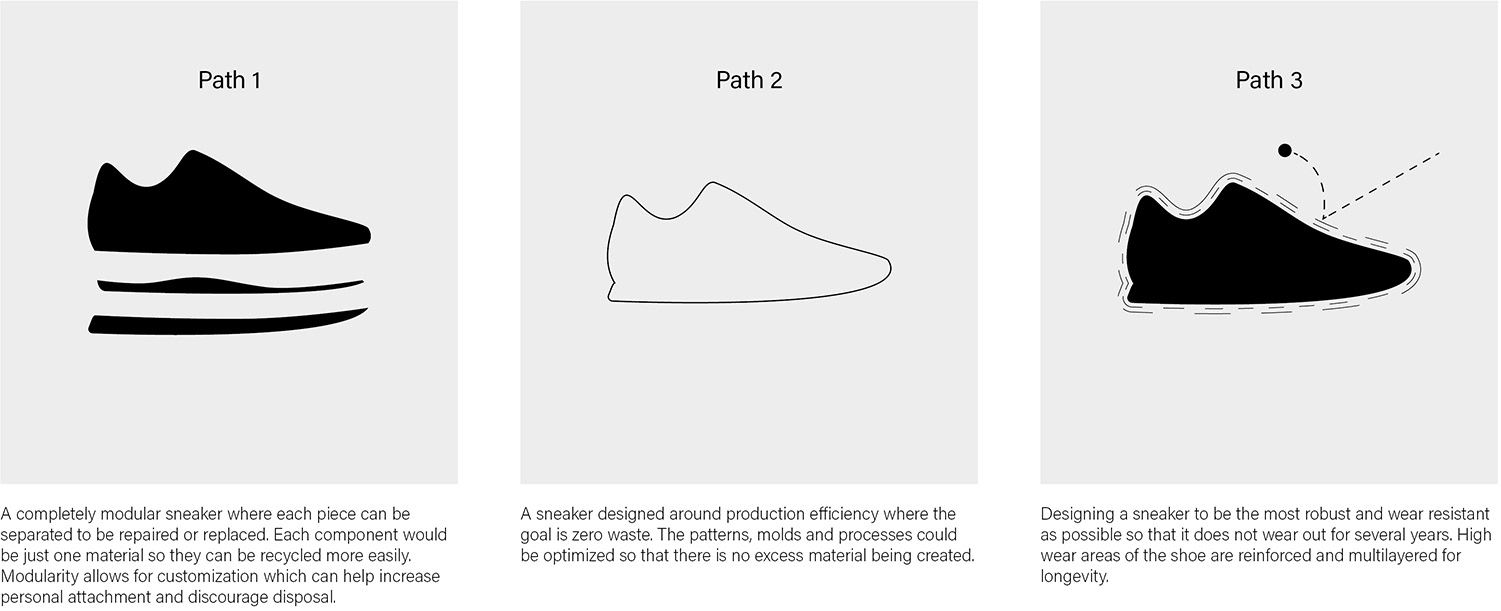
These design pathways are not mutually exclusive and could be combined and considered in any path. For this project, it was decided to focus towards Path 1 with a focus on modularity and repairability.
Material Selection
A breakdown of the materials used in each phase
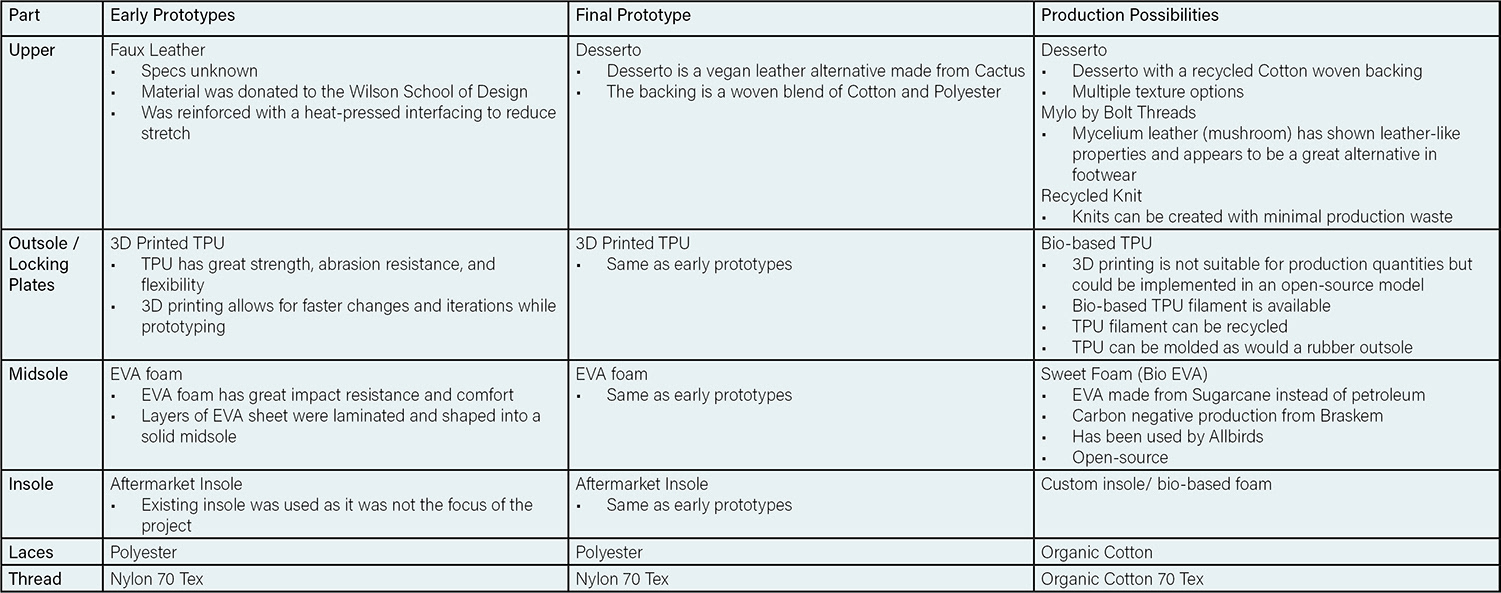
Initial Ideation
Sketching some preliminary ideas for a modular construction
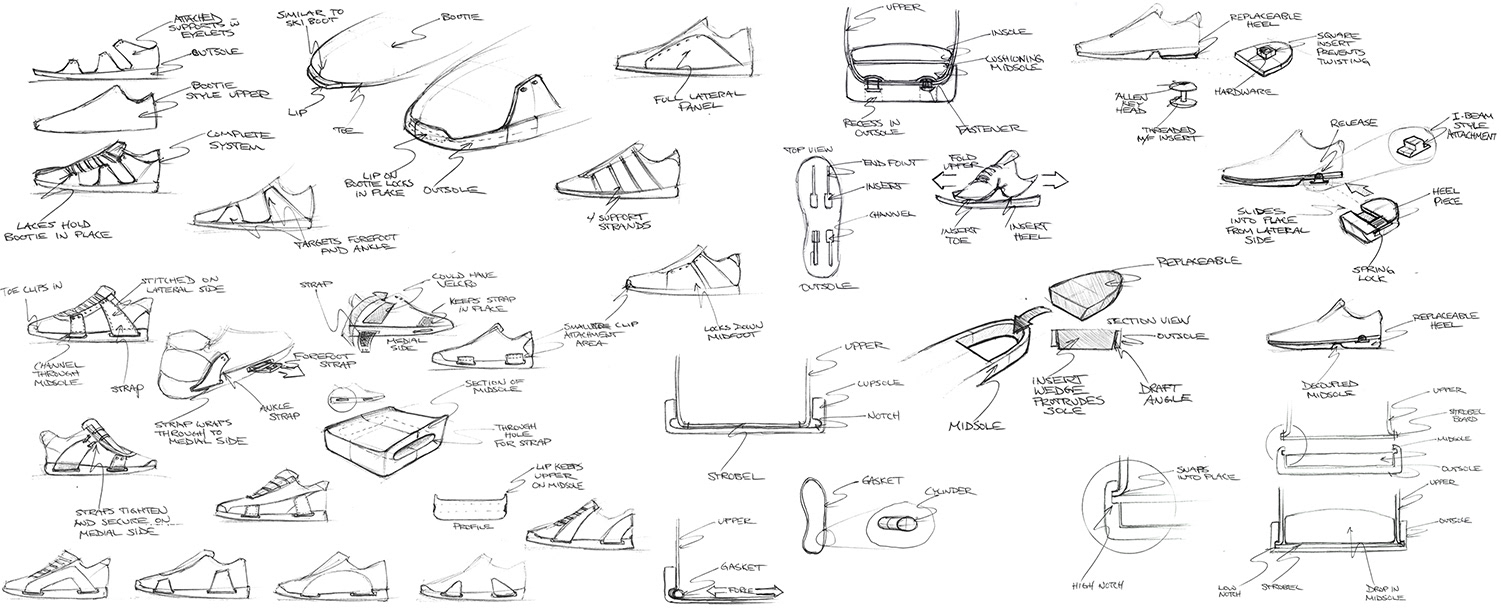
Concept Direction
Selecting a concept to proceed with for testing
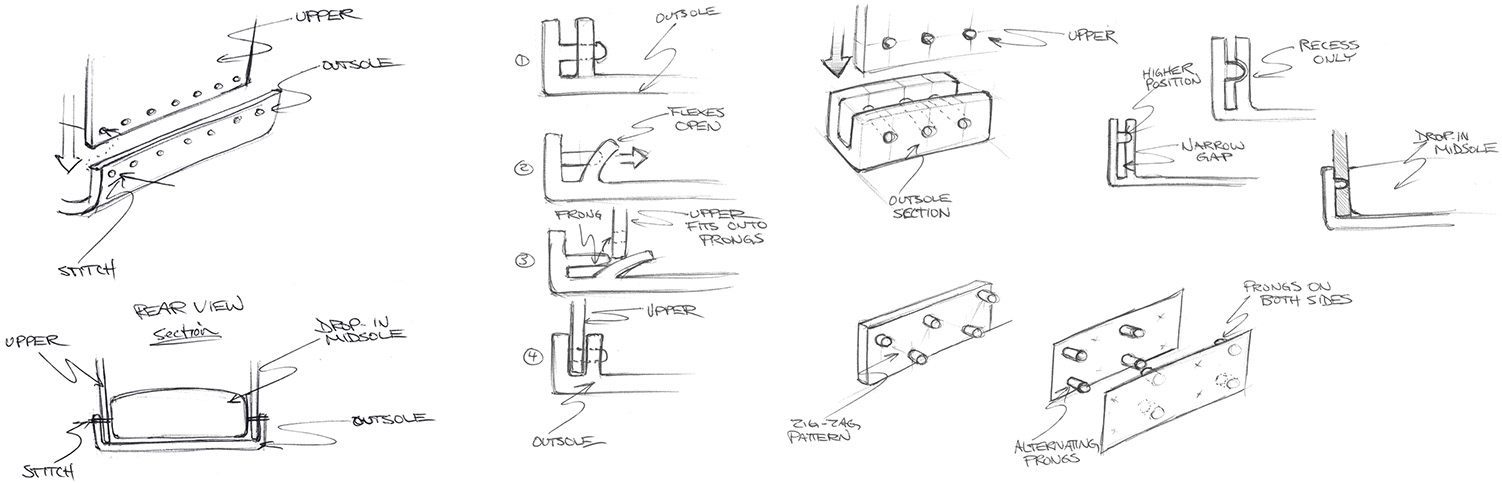
Rapid Prototyping
Using material swatches, silicone rubber, and parts of a deconstructed sneaker to test concept viability
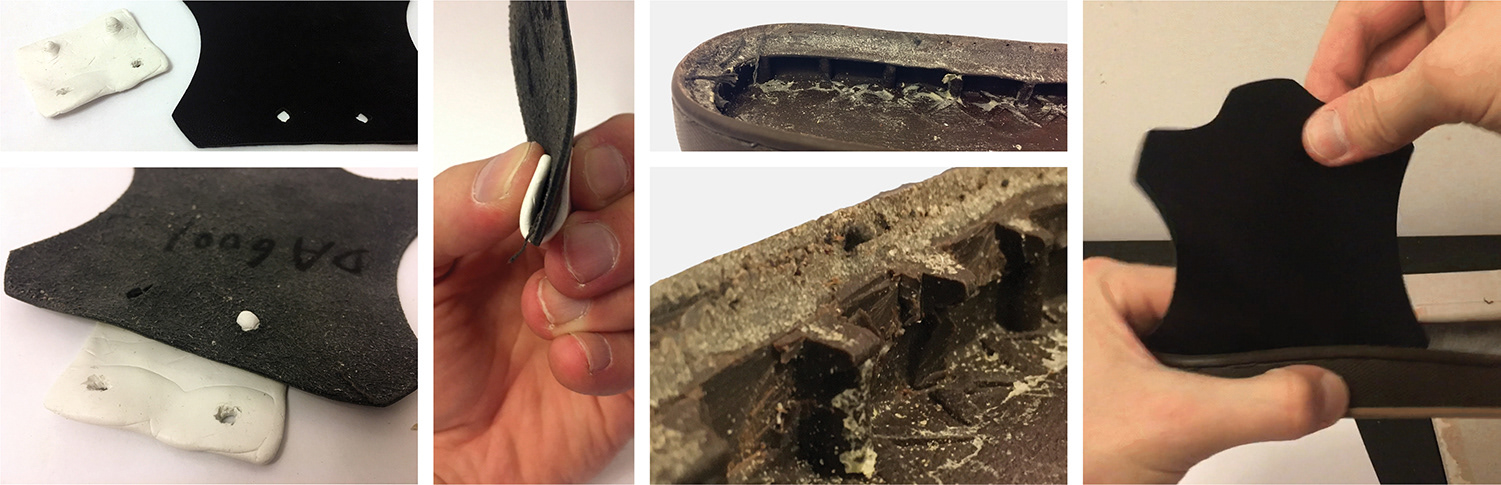
Design Concept
Presenting the design concept mid-year before starting with prototypes
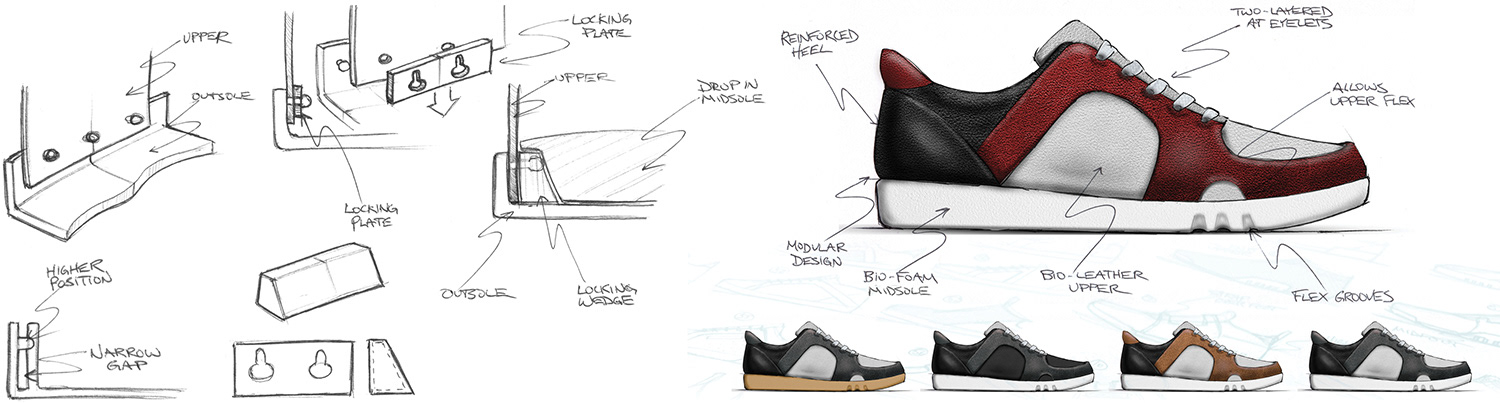
Last
Selecting, adjusting, and 3D printing a last
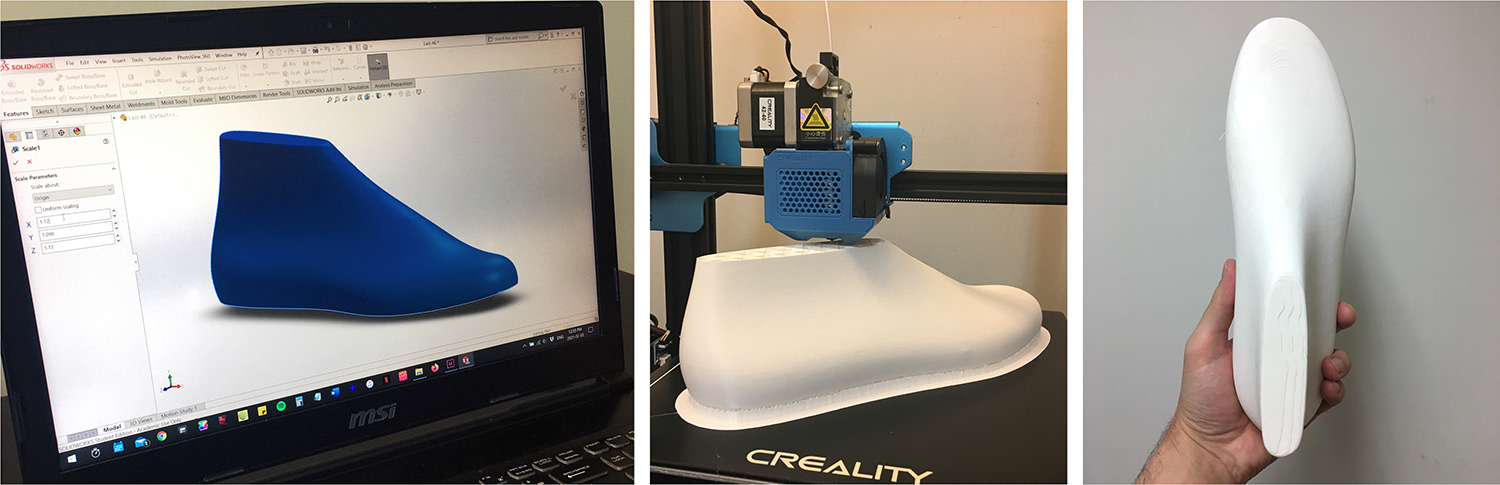
Outsole
Modeling and 3D printing outsole attachments for testing, and a completed outsole afterwards
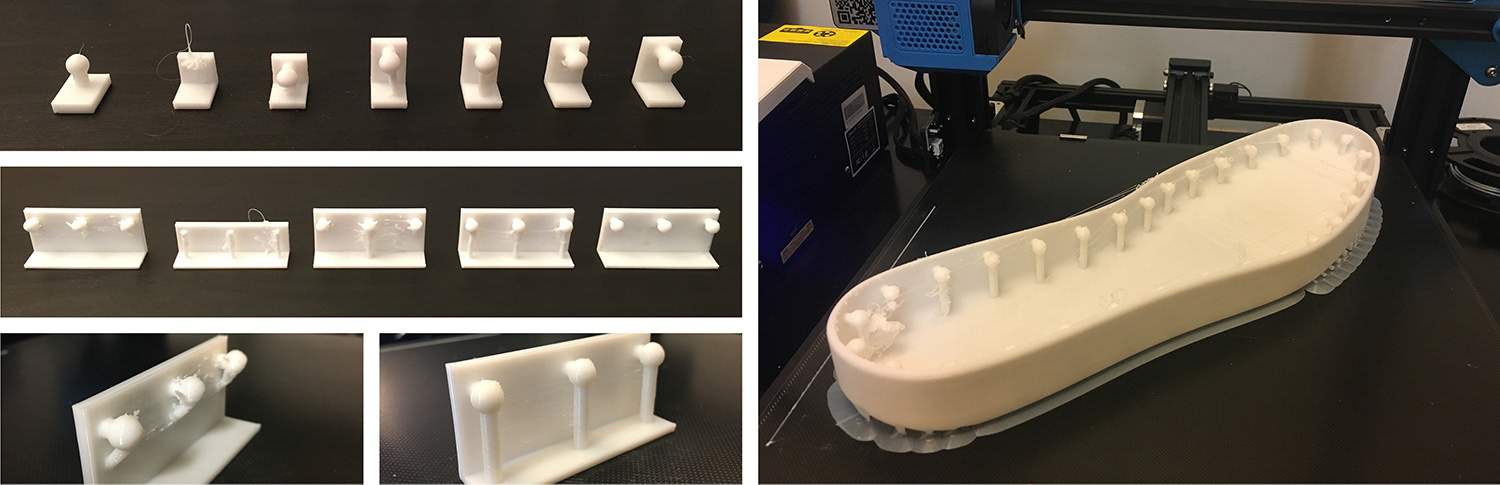
Locking Plates
Iterating on locking plate designs to be tested for strength and function
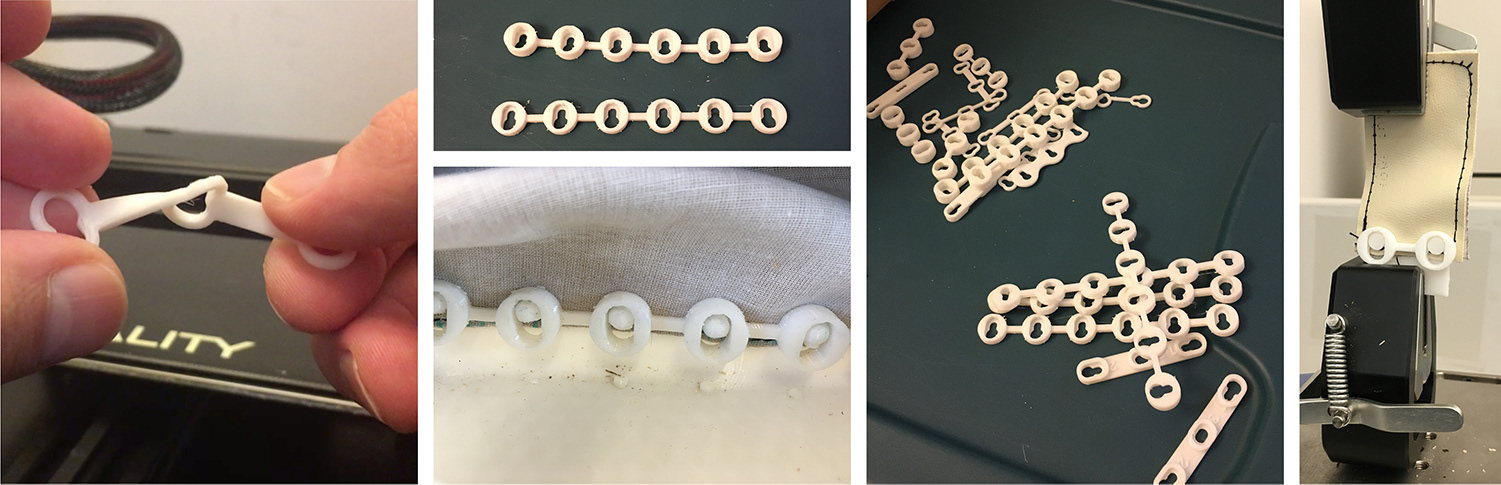
Midsole
Iterations and forming of the foam midsole
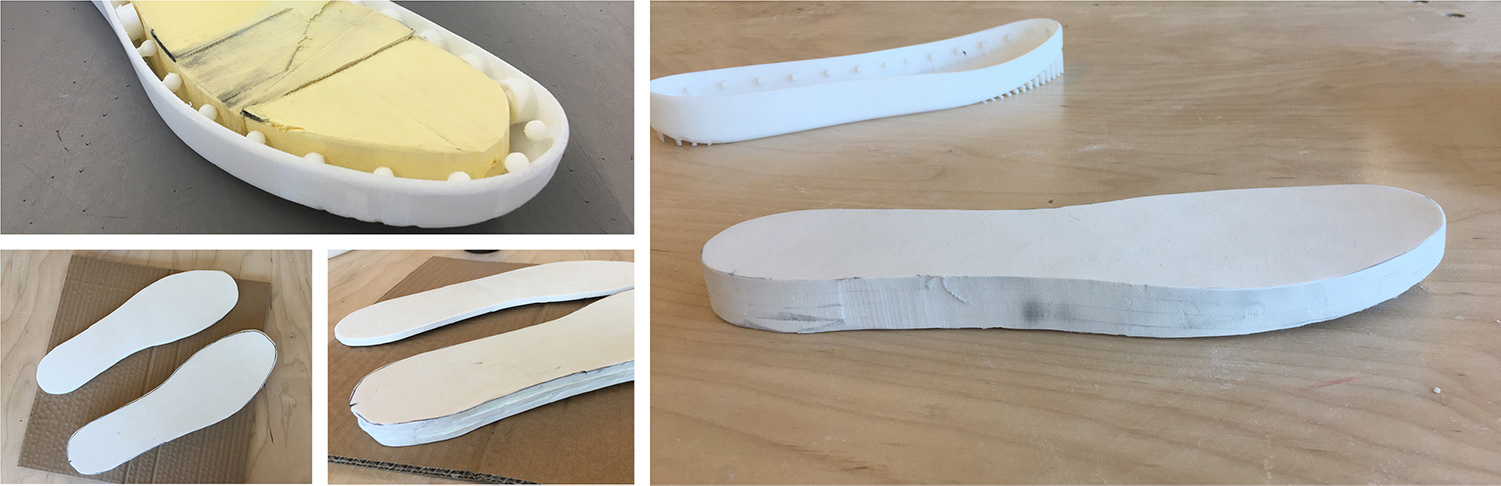
Upper
Tape-up of the last and pattern making the shoe's upper
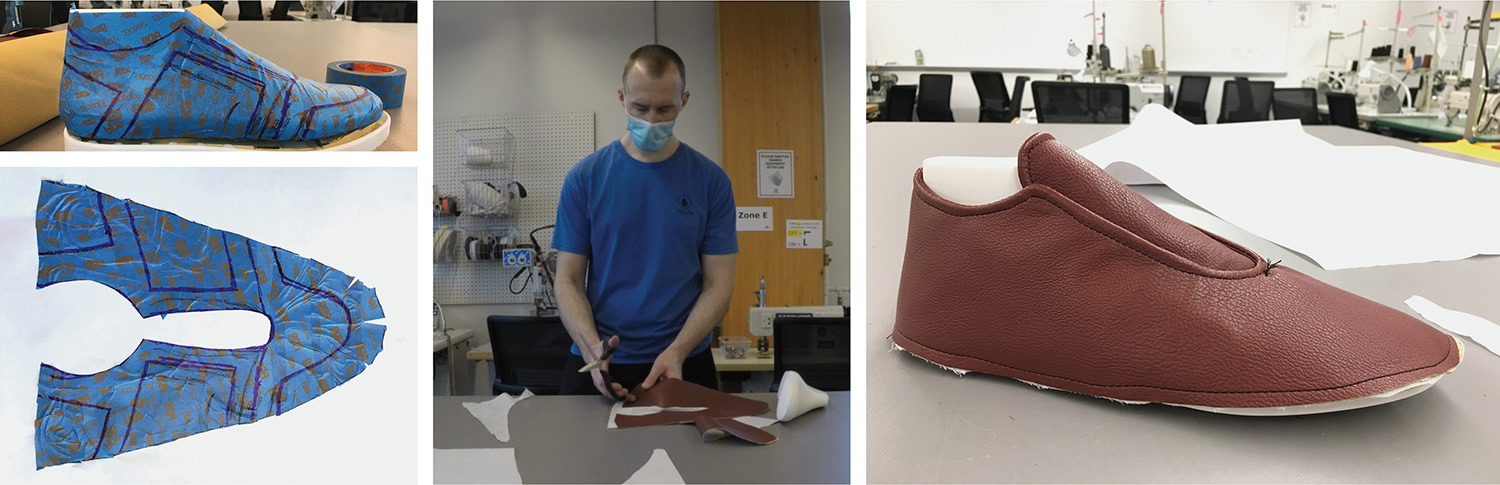
Prototyping
Developing the upper pattern for fit and style
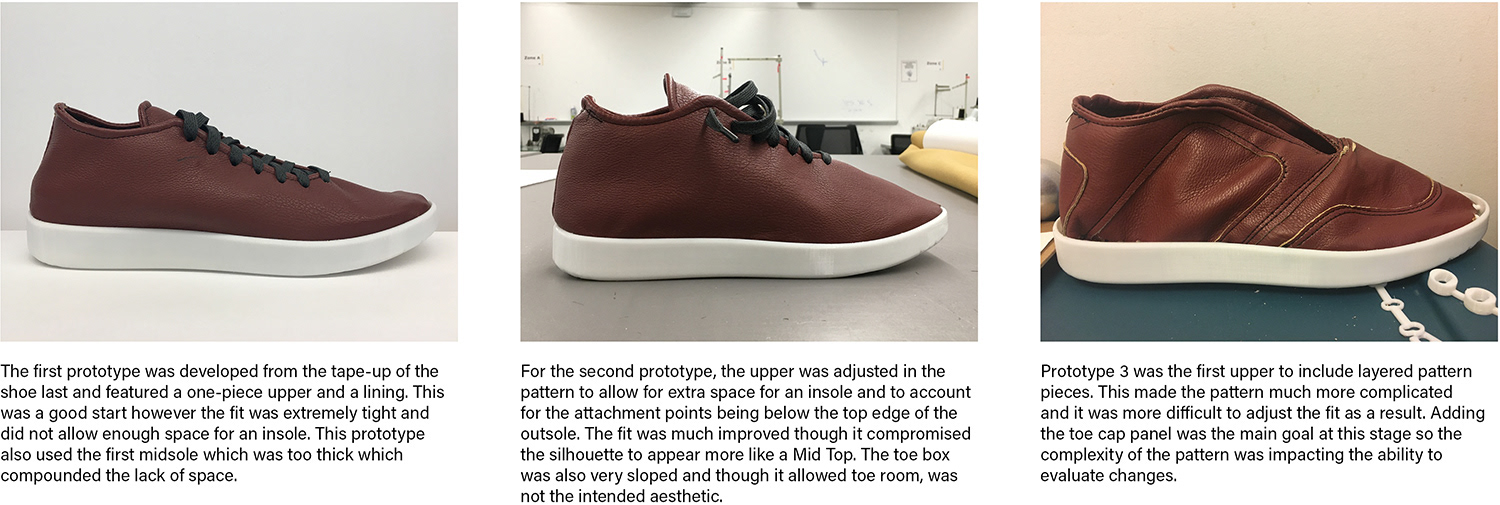
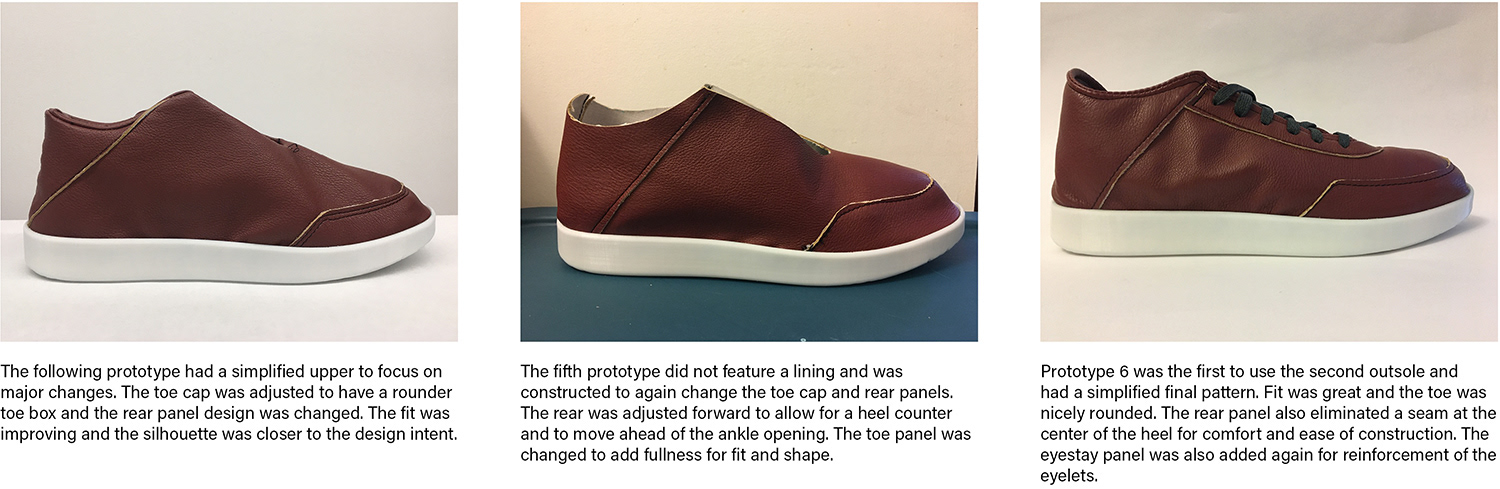
Final Construction
Making the final upper and debossed tongue logo
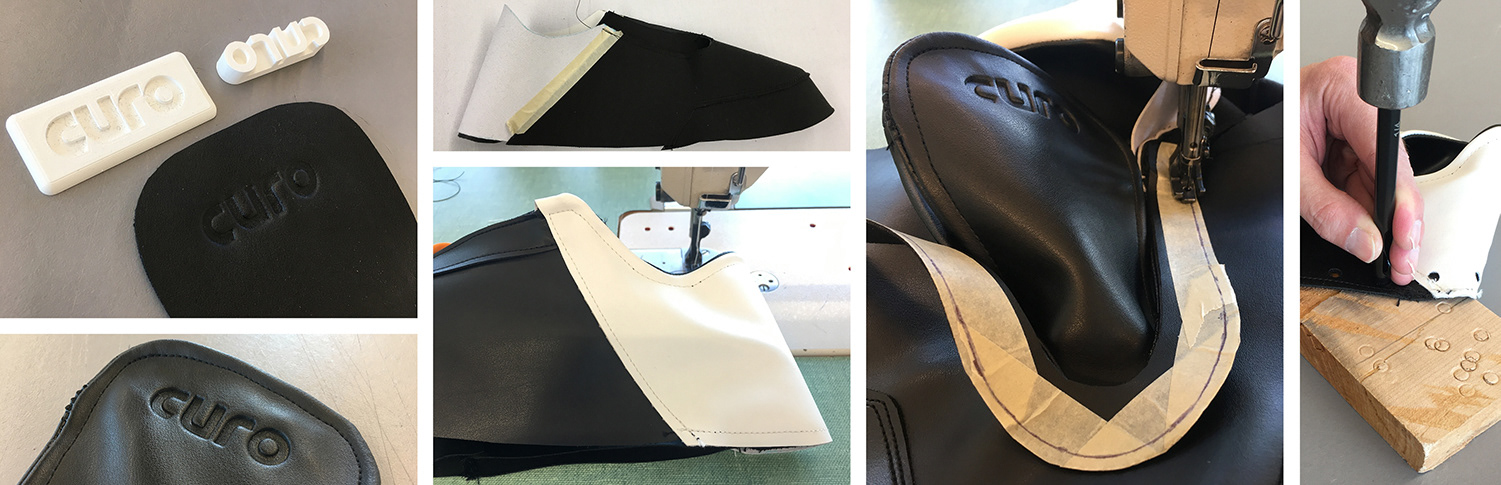
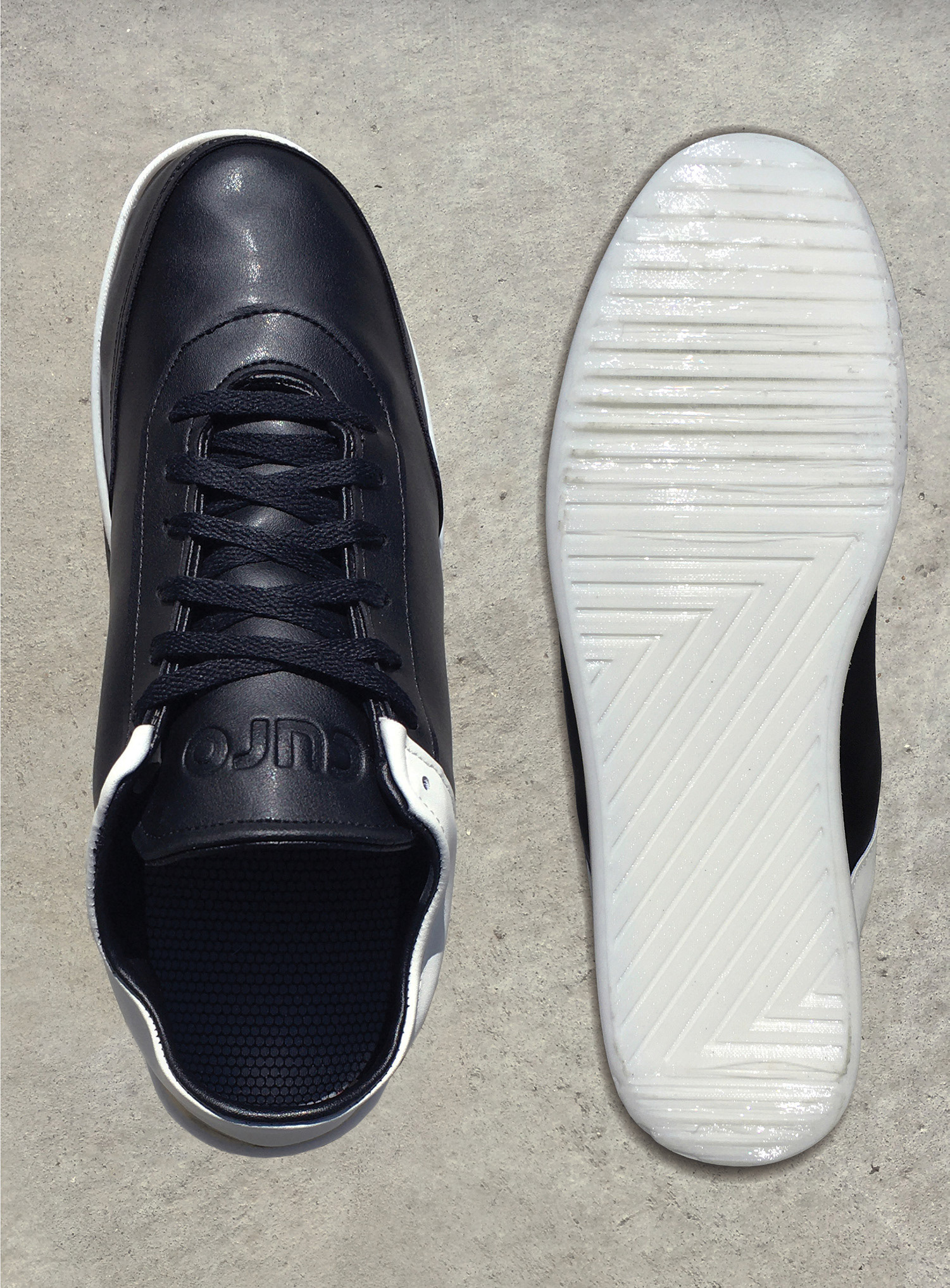